Clemente Parga has spent his career designing durable nuclear reactors, powerful rocket engines, and more. Now, he’s heading a team creating walls of liquid metal to harness fusion energy.
Lead Engineer Clemente Parga can describe the purpose of his work within three posters flanking his desk. One is a map of the world’s forests; another is a close-up of the sun; a third, a specialized periodic table displaying each element’s thermal properties.
“One is what we’re trying to protect, the next is what we’re trying to harness to create fusion, and the third is what we’re using to try to do it,” he explains.
For his entire career, Parga has pushed the frontiers of metallurgy. He’s safeguarded nuclear power plants by testing their limits and created alloys that could better withstand scorching temperatures within jet turbines. More recently, he supported the design of an engine for Blue Origin’s lunar lander capable of handling the extremes of space.
Now, at Zap Energy, Parga is once again operating on the edges of science, leading a team to develop a critical component in generating fusion energy: a looping and cascading wall of molten metal.
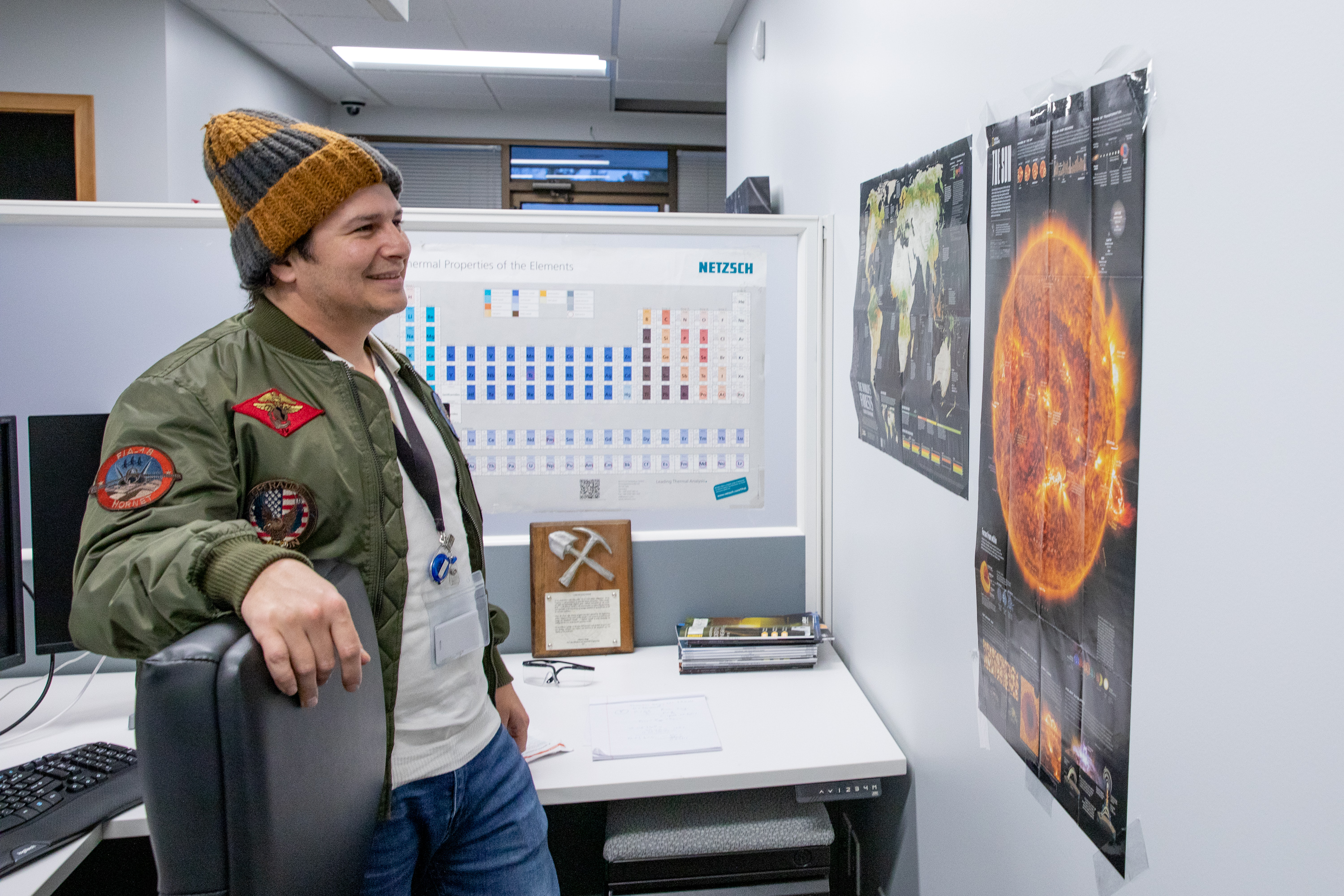
“If we can make fusion energy work, it will have so many overarching impacts on society and the environment,” says Parga, one of Zap Energy’s engineering managers. “This is the chance of a lifetime.”
‘Metals and minerals run in my blood’
Parga’s journey to Zap Energy took him from the border towns straddling the U.S. and Mexico, later to Southern France, Idaho, and finally, in 2018, to the Pacific Northwest.
Parga was born in El Paso but grew up in Ciudad Juárez. His great-grandfather founded a mine just north of Chihuahua City, which extracted, among other metals, lead – the very same element his great-grandson will melt as part of creating a fusion powerplant.
“I think metals and minerals run in my blood,” he suggests.
During his doctorate studies, Parga was exposed to the idea of fusion power for the first time. In 2010, he went to work at the CEA Research Center in Cadarache in France, which is also the campus of the fusion mega-project ITER – the International Thermonuclear Experimental Reactor.
Parga’s research centered on disaster response at nuclear power plants. In a twist of fate, Parga was just a year into his doctorate program when the Fukushima nuclear disaster occurred.
“From a scientific perspective it was a rare opportunity to learn from this disaster and find ways to assure this type of accident would never happen again,” Parga said.
After working at Idaho’s Transient Reactor Test Facility – a nuclear reactor designed to operate in extreme and accident-like conditions for training – he came to the Pacific Northwest as a materials and processes engineer for Blue Origin. There, he led the materials engineering for the liquid hydrogen-oxygen engines of the Blue Moon, a lunar lander capable of producing 10,000 pounds of thrust.
In 2021, he heard about an opportunity to join the Zap Energy team. It would bring him back to working toward clean energy. He jumped at the chance.
"Clemente combines an infectious personality with an incredible skill set, and all the fundamentals of a great leader," says Matthew Thompson, Zap's Vice President of Systems Engineering, noting Parga submitted his first patent application within weeks of joining the company.
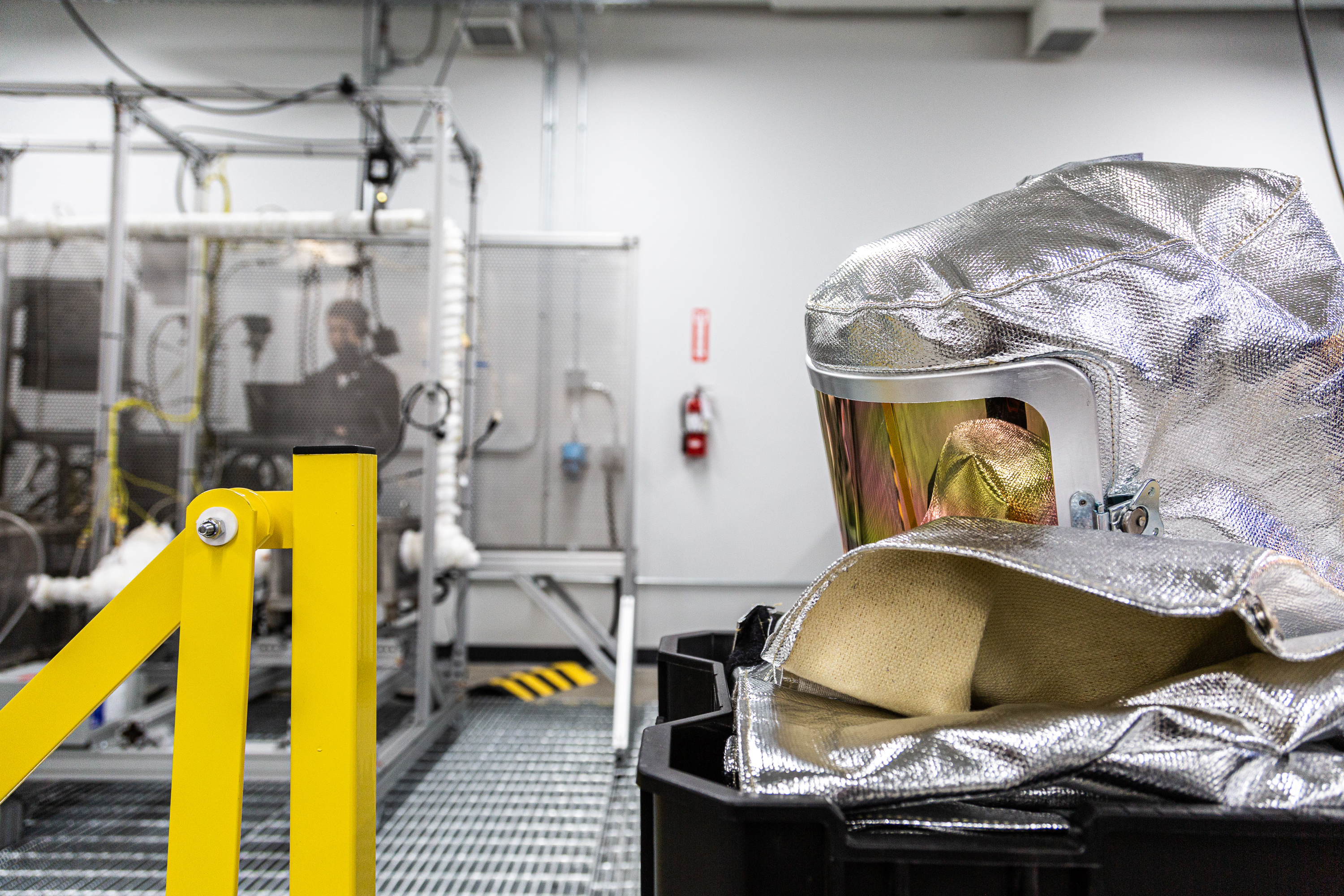
Building Zap Energy's molten metal walls
Creating – and sustaining – plasmas has been the focus of fusion development around the world. But what happens after the hydrogen nuclei fuse? Parga is leading the charge that will take that raw energy and convert it into usable heat and electricity.
He and Zap Energy’s team are creating a system of electromagnetically propelled molten metal that will loop the area around the company’s fusion core. The system will perform four critically important purposes. First, it serves as the conducting outer electrode for the electrical current that drives Zap’s plasmas. Second, the wall provides a shield against radiation. Because the molten metal is in motion, the wall is self-healing, and able to take on the extremely harsh conditions created by high-power electrical pulses and high-energy densities on the surfaces facing the plasma.
Third, the liquified metal will serve as a kind of conveyer belt to transport heat to a boiler that will ultimately drive a steam turbine, generating electricity.
Finally, the molten metal breeds tritium – a rare hydrogen isotope that can be extracted and put to work in Zap’s cores to fuel more fusion energy.
Zap Energy is already circulating liquified bismuth to simulate a fusion power plant’s molten metal wall. Parga's team plans to turn to a combination of lithium and lead as another potential candidate for the walls, elements which together create a higher probability of producing tritium than other molten metals.
Parga acknowledges he and his team have a difficult task ahead, but he’s optimistic. A passionate chef in his off-hours, he often uses cooking analogies within his work. In his grandmother’s kitchen as a boy, he fell in love with the smells and tastes of family dishes: egg and chorizo burritos for breakfast; heavy stews such as fabada, a bean stew from the Spanish region of Asturias, for supper. He sees parallels between metallurgy and the culinary, and the tinkering that goes into each.
“In cooking you have these main elements or components in your dish that you put together, but in the end you might add a little bit of this or that, like adding a little bit of salt or pepper to a stew," he said. "Designing metals is similar, add too much or too little of an ingredient and it makes a big difference.”
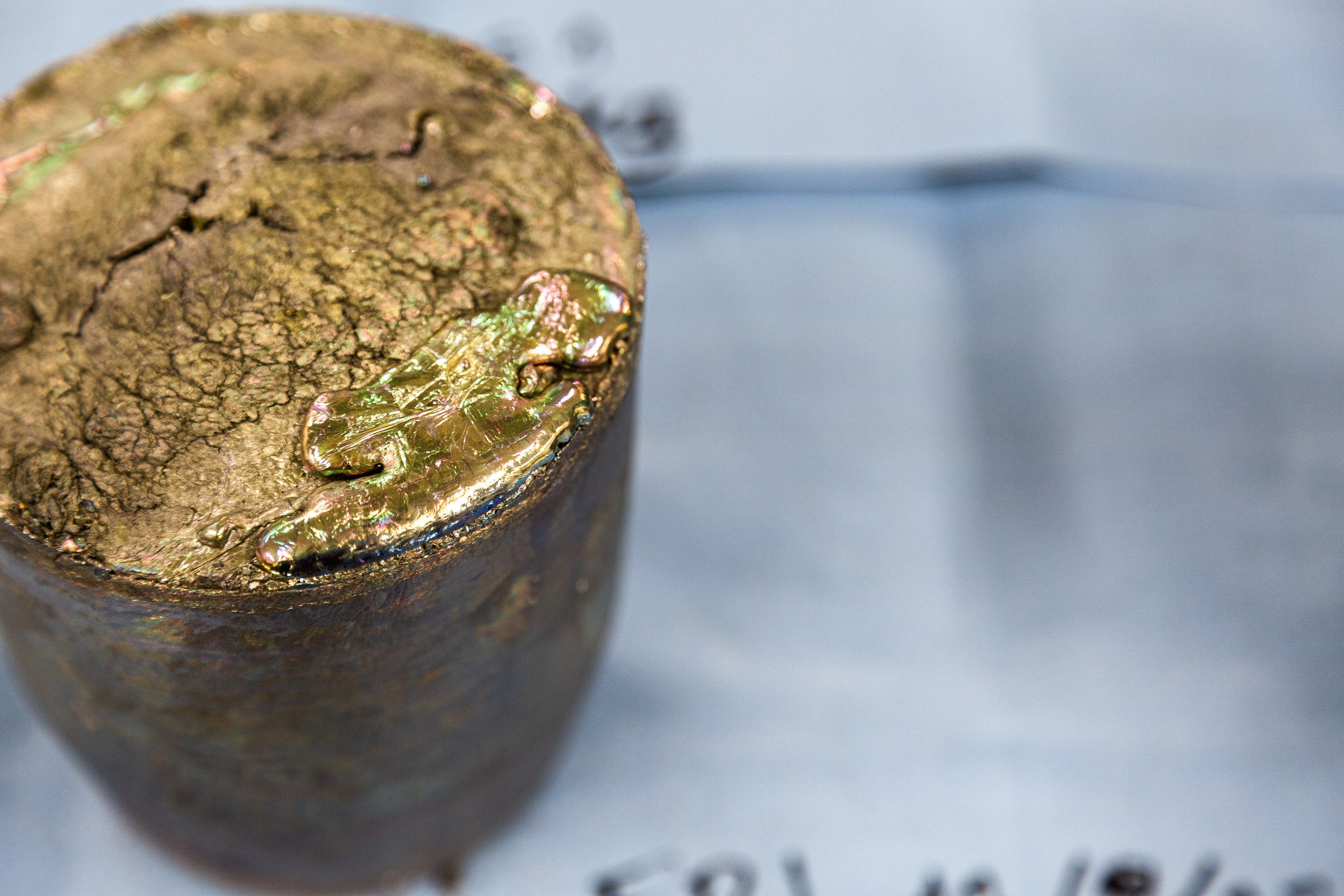
He’s never lost that love of cooking. An avid gardener, he keeps a collection of succulents and cacti to remind him of home on the border of Mexico and Texas. A favorite pastime is camping, sitting by a fire, and watching the flames dance. He tells the story of the paradigm shift when humanity harnessed the heat from fire; fusion, he believes, could be another such shift.
“Nature is resilient but so sensitive,” he said. “It’s something that we really need to protect. If we make fusion energy work, having a cleaner, cheaper source of energy will help our world and will improve people’s quality of life.”